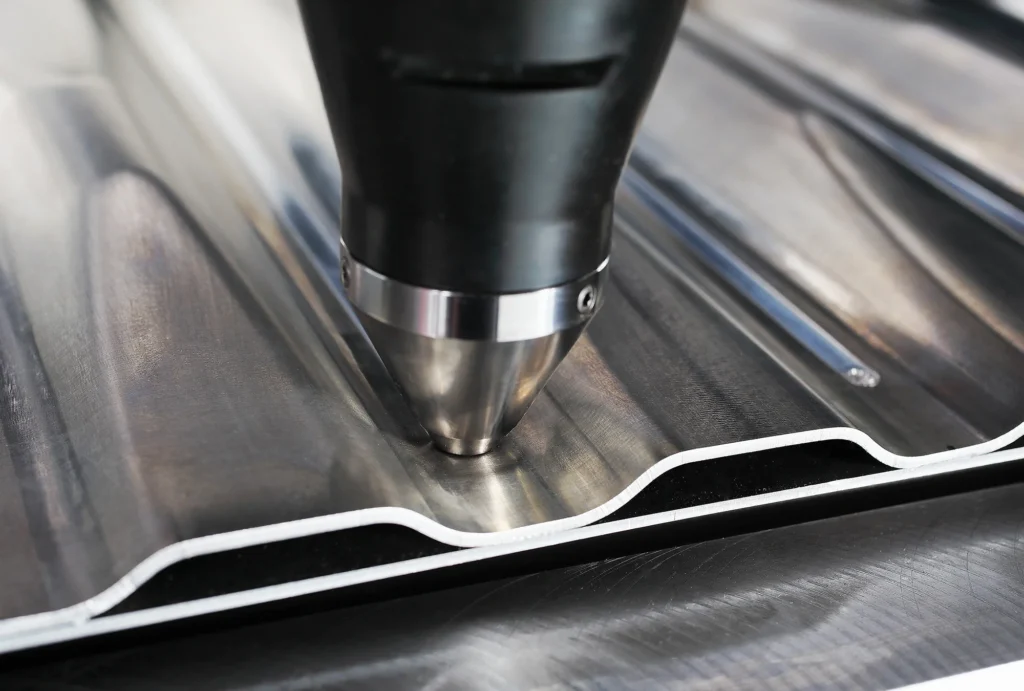
Friction Stir Welding is one of the revolutionary techniques adopted in automobile sector as it provides optimum technical solutions for lightweight materials joining. FSW stands for Friction Stir Welding, another TWI innovation came to existence in 1991, this method of welding is a solid-state process with the application of a non-consumable tool that produces heat through friction.
When the tool is in the plane of the edge of the plates which are clamped the material is plastically deformed leading to the formation of a solid phase weld. This technique is useful especially in dealing with aluminum alloys that are significantly utilized in present day vehicles; it is currently being utilized to other metals such as titanium to meet the emerging needs in the automotive industry for lighter, stronger and more durable parts.
Opportunities and uses of friction stir welding in the automobile industry
There has been a growing demand on automobile manufacturers to develop cars that are lighter to enable them to consume less fuel but at the same time provide increased safety features. These challenges are overcome by Friction Stir Welding because it expands the potential for lighter, stronger materials such as aluminium and titanium which can prove to be problematic when welding fusion processes are employed. This technology is now integral to various automotive applications, including:This technology is now integral to various automotive applications, including:
- body-in-white structures: FSW is employed in the assembly of BIW structures from aluminum panels and extrusions, enhance crash worthiness while at the same time seeking to achieve weight reduction.
- battery trays for electric vehicles: FSW is the most suitable process to fabricate battery trays because the process produces strong and leak-proof://labs that shield battery cells in EVs.
- heat exchangers and radiators: Thus, appropriate joints are provided by FSW process for heat exchangers and radiators, which are essential for handling thermal cycles and pressure associated with operating condition.
- chassis components: Aerospace-grade FSW makes it possible to weld Chassis components of cars made of titanium, thus increasing vehicle stiffness and handling capabilities.
Advancing automotive innovation through friction stir welding
The ongoing evolution of friction stir welding in the automotive sector signals a promising future for vehicle design and manufacturing. As research continues to overcome current challenges, such as improving tool durability and expanding the process to a broader range of materials, FSW is poised to play a pivotal role in the development of the next generation of vehicles.
From lightweight electric cars to high-performance sports vehicles, the ability to create stronger, lighter, and more efficient components will not only enhance vehicle performance but also contribute to sustainability by reducing energy consumption and emissions. As automakers strive to meet global demands for innovation and environmental responsibility, friction stir welding stands out as a key technology driving this transformation.
Future prospects and challenges
The constant development toward friction stir welding in the automotive industry means the bright future will appear to vehicles design and production. Considering that current research is still a way off the challenges mentioned above, including enhancing tool wear and resistance, and applying FSW to a variety of materials, it becomes clear that FSW has great potential to shape the next generation of vehicles.
Starting from electric cars to sports cars the designing of cars that have lighter weight, high strength and efficiency will not only improve the capability of cars to perform but also lead to use of less fuel and energy. In this global fight for creating vehicles that progresses technologically and shows environmental consciousness, friction stir welding is making a unique contribution to this change.