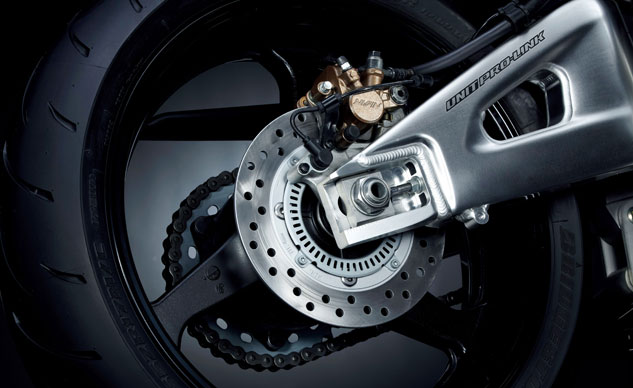
While many private vehicle developers are hard at work, making the cars faster and shinier, truck development companies are focused on navigating the ever-changing standards and regulations landscape. Due to the nature and risks involved in the trucking industry, there are many more regulations to be met than in the personal automobile space. This is probably because a heavy vehicle can cause a lot more damage and put more lives at risk if involved in an accident.
While the payload capacity and fuel efficiency of a commercial truck are the most sensitive areas as pertains to truck revenue, the bulk of technology developers focus on the truck’s safety features. Companies, today are more interested in a trucks’ safety features because, in the age of social media and free press, truck failures and fatalities can cause more damage to your revenue than a few more gallons on the mile.
What is the CVDC?
CVDC stands for the ‘Cambridge Vehicle Dynamics Consortium’ which is a joint task force – so to speak – of Cambridge University engineers and a group of companies from the heavy truck industry. This consortium is a collaborative initiative with a joint goal to improve heavy goods vehicles. The consortium’s ever-expanding membership currently consists of about 13 member companies including Firestone, Volvo Trucks, Wincanton, Camcon, Goodyear, Denby Transport, Mektronika Systems, MIRA, Poclain Hydraulics, SDC Trailers, Tinsley Bridge, SIMPACK and Tridec BV.
The CVDC uses advanced technology and computer simulations to research ways to improve heavy trucks performance and safety features on the road. With constant input and support from the industry members, the Cambridge University engineers are able to come up with new solutions and prototypes and test them in the field with virtually no delays due to funding or bureaucracy.
The CVDC Pneumatic Slip-Control Braking System
There hasn’t been much noise around braking systems in heavy trucks since the development of the Anti-locking Brake System (ABS) and the Electronic Brake System (EBS) which made remarkable improvements to the braking efficiency and maneuverability of trucks.
The ABS and EBS work on the same basic principle of applying and releasing the braking pressure on the wheels of the truck at quick intervals to allow the driver to control or swerve the truck while preventing it from locking and slipping on the road. The main difference between the ABS and EBS is that the EBS uses electronic signals to control the braking pressure.
The novel Pneumatic Slip-Control Braking system was developed at Cambridge University, UK under the leadership of Professor David Cebon and his colleague Dr Graeme Morrison in collaboration with brake manufacturer Haldex as part of the CVDC group. This technology comes as one of the biggest breakthroughs in brake technology as it boasts to reduce stopping speeds by 15% to 17% and saves on 22% to 30% of the air used in the braking system to bring a truck to a halt when compared to the conventional ABS systems. This system can also wheel slip demand tracking by up to 62%.
Most improvements in the brake development sector of modern trucks have been limited to reducing the driver’s reaction time and workload by introducing proximity sensors and Automatic Emergency Braking (AEB) solutions. Professor Cebon’s solution has produced such tangible results that Haldex has already started developing prototypes and testing them in real-world situations.
How it Works
Professor Cebon and his team were able to achieve this breakthrough in braking efficiency by re-engineering the conventional EBS system to identify its bottlenecks and potential points of improvement. This was no easy feat, and the team has gone through 10 years and three PhD students to come up with this viable solution.
The main change the CVDC team made to the EBS system was to improve the delivery speed of air pressure to the brake chamber and to minimize actuator delays. The team found that the current brake actuator valves are not very efficient and use too much air to achieve the necessary brake pressure because they take about 40 milliseconds to open and close.
Professor Cebon’s team found that by replacing the 40-millisecond valves with 15-millisecond valves, there was a significant reduction in stopping distances. They took a step further and used fast bi-stable 3-millisecond valves to reduce the open and closing times to less than a tenth of the original speed. This led to an even more significant improvement in the braking system’s performance. Upping the speed again to use 1-millisecond valves did not do much to improve the performance further so the team settled on implementing the 3-millisecond bi-stable valve solution.
The feat achieved by Professor Cebon and his team at the CVDC was presented and warmly received by the truck and trailer engineers at the 14th Heavy Vehicle Transport Technology in Rotorua, New Zealand earlier this year.